Hello people,
I am stuck with putting this Hobart back into service. I rescued it from the scrap pile and am almost there but I need some better minds than mine.
This welder was missing the local/remote toggle switch and also the name plate that contains the specs for it. I found 4 cut wires behind the panel where the switch was with no clue as to how to terminate them. The 4 wires are color coded two yellow, red and green. The two yellow ones go to the panel rheostat and the remote plug respectively. The red one goes to the second commutator from the front and the green one goes to the first commutator from the front. I tried all combinations I could think of to see if it had any effect on the power output of the welder, it didn"t. I think it needs to be flashed, but do not want to do this until I have the wiring connected properly.
I ordered a manual for a G-3010 but the wiring diagram is different and instead of 4 wires to the local/remote switch, it shows six. Plus my engine is a Willy"s flat head 4 cylinder, the G-3010"s I"ve seen pictures of have a Chrysler six slant six. Makes me think that either mine is NOT a G-3010 or my version is earlier than when the ones I"ve seen pictures of.
I traced each of the 4 wires and drew a diagram so that others might be familiar with what I am facing and know how to deal with these wires. I have tried to test weld with it but so far it refuses to generate welding power (or ac power to the outlets). I don"t know if this is because it needs to have the local/remote wires terminated properly in order to complete a circuit or because it may need to be "flashed" (or both). I was gong to "flash" the generator according to instructions in the manual I ordered when I discovered that 4 of the 8 brushes were not connected to the wiring, the pigtails had fallen out of the brushes. I ordered new brushes all around and installed them yesterday. This where I am at now. The drawing shows one connection where the green and white wire terminates at a junction with 7 other wires. I don"t know what this part is called but there is a picture of this included that might help figure this out.
The engine runs fine, the welder does not weld. Also the AC ammeters, voltmeters are not working and appear damaged. I am looking for a source for these, but this should not prevent the welder from welding, only showing the power readings.
While I"m at it I need to find a gas cap for it as all it has is a home made cap that sits on the gas filler neck. Does anyone know by looking at the pictures?
Any help will be greatly appreciated.
Tony
I am stuck with putting this Hobart back into service. I rescued it from the scrap pile and am almost there but I need some better minds than mine.
This welder was missing the local/remote toggle switch and also the name plate that contains the specs for it. I found 4 cut wires behind the panel where the switch was with no clue as to how to terminate them. The 4 wires are color coded two yellow, red and green. The two yellow ones go to the panel rheostat and the remote plug respectively. The red one goes to the second commutator from the front and the green one goes to the first commutator from the front. I tried all combinations I could think of to see if it had any effect on the power output of the welder, it didn"t. I think it needs to be flashed, but do not want to do this until I have the wiring connected properly.
I ordered a manual for a G-3010 but the wiring diagram is different and instead of 4 wires to the local/remote switch, it shows six. Plus my engine is a Willy"s flat head 4 cylinder, the G-3010"s I"ve seen pictures of have a Chrysler six slant six. Makes me think that either mine is NOT a G-3010 or my version is earlier than when the ones I"ve seen pictures of.
I traced each of the 4 wires and drew a diagram so that others might be familiar with what I am facing and know how to deal with these wires. I have tried to test weld with it but so far it refuses to generate welding power (or ac power to the outlets). I don"t know if this is because it needs to have the local/remote wires terminated properly in order to complete a circuit or because it may need to be "flashed" (or both). I was gong to "flash" the generator according to instructions in the manual I ordered when I discovered that 4 of the 8 brushes were not connected to the wiring, the pigtails had fallen out of the brushes. I ordered new brushes all around and installed them yesterday. This where I am at now. The drawing shows one connection where the green and white wire terminates at a junction with 7 other wires. I don"t know what this part is called but there is a picture of this included that might help figure this out.
The engine runs fine, the welder does not weld. Also the AC ammeters, voltmeters are not working and appear damaged. I am looking for a source for these, but this should not prevent the welder from welding, only showing the power readings.
While I"m at it I need to find a gas cap for it as all it has is a home made cap that sits on the gas filler neck. Does anyone know by looking at the pictures?
Any help will be greatly appreciated.
Tony
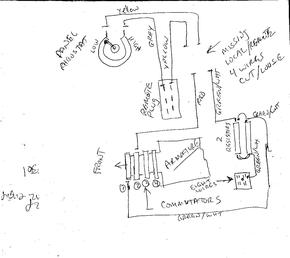
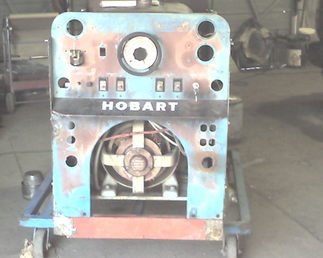
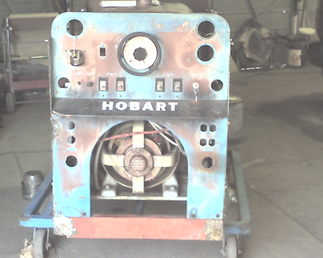
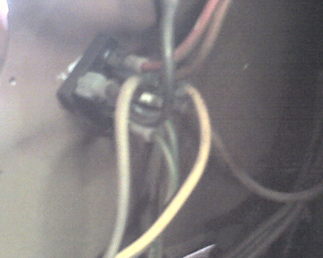
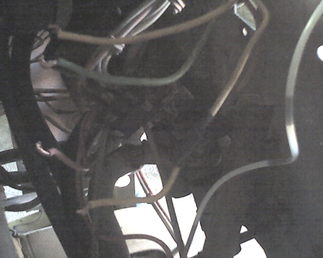
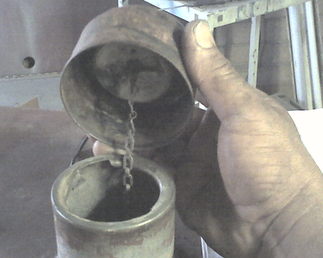