I've got a wallowed out pin mount bracket that I'd like to repair. What'd be the best way? I see three options. WHat others are there?
1. Replace whole bracket - need to drill/machine hole in bracket. I don't have the best tooling to drill hole properly
2. Bore out hole oversized and weld in an insert - Need to get/make insert
3. Fill wallowed out area with weld filler - need to get something to take up pin space when welding.
I have welding machines, a plasma cutter, etc.
How would you go about doing this?
1. Replace whole bracket - need to drill/machine hole in bracket. I don't have the best tooling to drill hole properly
2. Bore out hole oversized and weld in an insert - Need to get/make insert
3. Fill wallowed out area with weld filler - need to get something to take up pin space when welding.
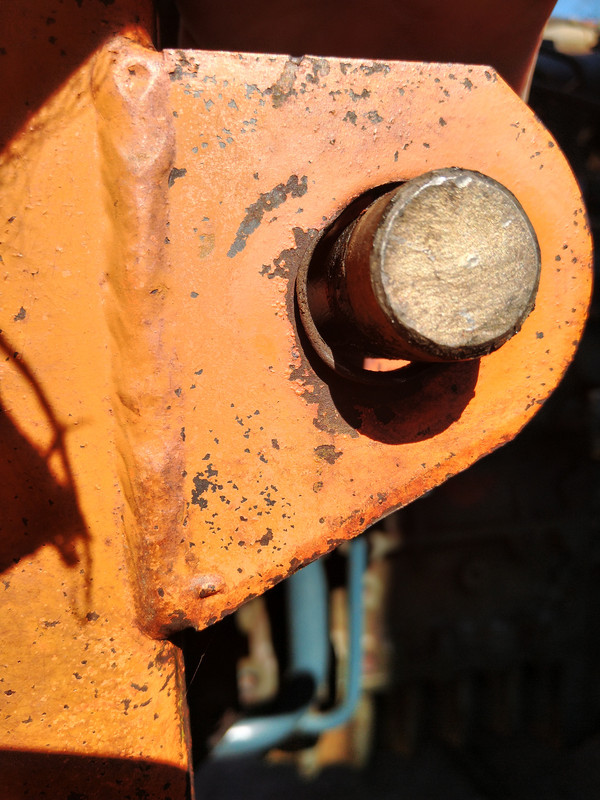
I have welding machines, a plasma cutter, etc.
How would you go about doing this?